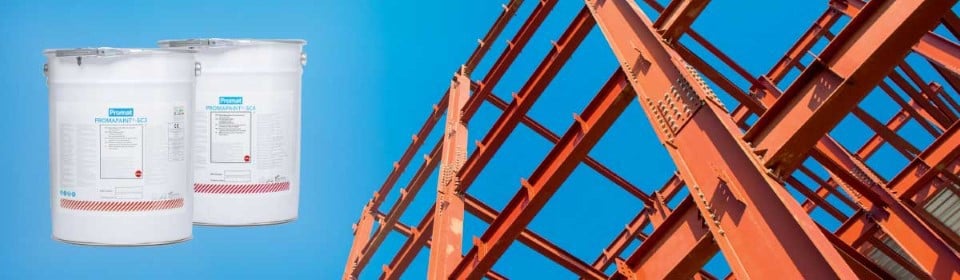
Steel structures can provide designers with increased flexibility in comparison with traditional construction materials, and are becoming widely used in modern building construction thanks to their exceptional properties such as high mechanical strength, low construction weight, ductility, short execution times, being relatively simple to change by adding or removing construction elements and an increasingly important feature – the ability to recycle old or used profiles.
However, due to the deterioration of mechanical properties, especially load-bearing capacity, with elevated temperature (e.g. in case of fire, where it can easily reach 500°C or more) deformation and collapse of the structure can occur very quickly. It is thus essential that steel elements have the necessary fire resistance to prevent a collapse caused by fire, avoid buckling or at least do so with some delay, and thus gain evacuation time for the occupants and the rescue teams.
Several protective measures have been developed with one thing in common – they must all be considered in the planning stage, because such measures depend on several technical factors, such as the expected load or other forces, expected maintenance, appearance, economic aspects, weather-related factors, difficulty of installation, and many other elements. One such solution is fire protection using intumescent fire protective coatings (also known as reactive coatings).
Why would you choose a fire protective coating? Intumescent coatings allow for easy and fast application during construction and provide an attractive finish that does not compromise intricate designs and shapes created from steel, giving clients an aesthetic benefit where exposed steelwork is an integral part of the design or when cladding with boards is too complex. This allows maximum architectural expression for structures such as airports, stadiums, leisure facilities, hospitals and office buildings. That is why intumescent coatings represent an increasingly used way of providing passive fire protection to steel structures used in modern architectural designs.
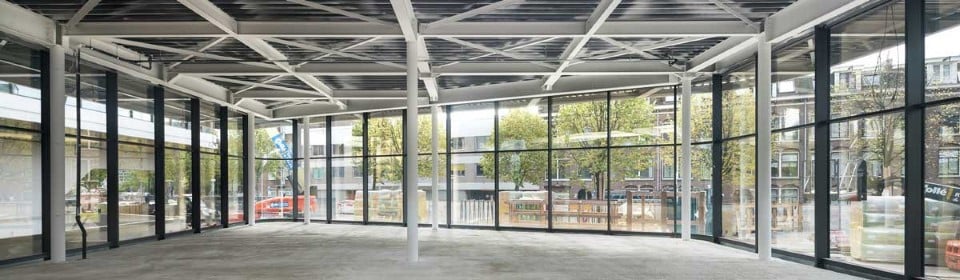
To ensure the load-bearing capacity of the structure for 90 minutes or more, the most commonly used protection with boards is also the most affordable. For shorter fire protection time periods, we can choose from several types of protection, one being Promat’s reactive fire protective coatings.
Application costs and durability have been optimized in recent years through advances in product development and material innovations resulting in thinner solutions. Add this to the increasing number of suppliers entering the market and this system has now become a frequently used method for steel fire protection, alongside board-based systems.
Which intumescent coating to choose for your project?
Thanks to its wide experience in fire protection and, more specifically, in the protection of load-bearing structures, the R&D department of Promat has designed and developed two intumescent coatings consisting of resins and fillers with different performances and characteristics, to meet all the market needs. Both are fully tested according to European Standard EN 13381-8 (and can be used for profiles with an extremely high section factor (Ap/V).
PROMAPAINT®-SC3 is a water borne intumescent paint, CE marked by an ETA and tested for steel structures and concrete components according to European standards (EN 13381-8 for steel and EN 13381-3 for concrete). The coated steel or concrete components achieve fire resistance classes from R(EI) 15 to R(EI) 180. This product is mainly used for the high fire resistance classes and for hollow section circular and rectangular steel sections (both beams and columns).
PROMAPAINT®-SC4 is a single component intumescent paint in water emulsion consisting of synthetic resin especially formulated for steel structures, CE marked by an ETA and tested according to European standards for steel, concrete and composite loadbearing slabs (EN 13381-5). The coated steel components achieve fire resistance classes from R 15 to R 120. This product is mainly used to achieve medium-low fire resistance with excellent performance for R 30-60 on an open steel profile. Both have a wide variety of uses inside of buildings and in open halls, and are intended for all conditions (internal, semi-exposed and exposed) according to ETAG 018-2 used as EAD and the most recent EAD 350402-00-1106.
Advantages and performance
PROMAPAINT® products can be specifically used in areas where the application of solvent-based products is perceived to be an environmental hazard, such as hospitals, health care centres, schools, public buildings or in fact any building that is occupied or attached to occupied areas, and provide the following benefits for the customer:
- aesthetic benefits for projects where the exposed steel structure is an important design feature (the steel elements remains visible)
- thin and seamless result, because of lower application layer thicknesses
- up to 750 microns (Dry Film Thickness) in one coat by spraying
- easy to apply
- can be repainted and repairs do not compromise the fire resistance, according to the official fire tests
- durable, lightweight coating
- suitable for galvanized steel structures
- topcoat not necessary for indoor applications with low humidity (Z2)
- fully exposed (X) with suitable topcoats
- tested and approved for open and hollow steel sections for fire protection up to R(EI) 180 (PROMAPAINT®-SC3) and up to R 120 (PROMAPAINT®-SC4)
- improving the fire resistance of loadbearing brick and reinforced concrete members (only PROMAPAINT®-SC3)
- solvent free, extremely low VOC
System performance and thicknesses
The property of being intumescent means that the material swells as a result of being exposed to heat, thus increasing in volume and decreasing in density. Specifically, an intumescent paint is a coating that reacts to heat by swelling in a controlled manner, expanding between 40 and 200 times its original thickness, producing a carbonaceous char formed by a large number of small bubbles that act as an insulating layer to protect the substrate.
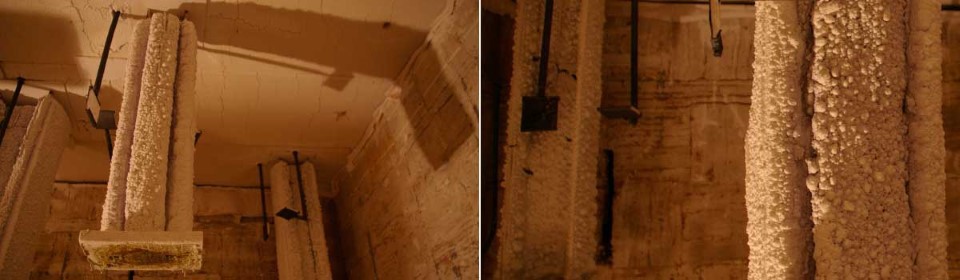
The key use of intumescent products is the prevention of the structural collapse of a building, which can occur if load-bearing elements reach a critical state. For steel, this is linked to the critical temperature, defined as the temperature at which the load-bearing capacity becomes equal to the effect of the applied loads (so the steel element is very close to collapse). The critical temperature of steel can vary from 350 °C to 750 °C, depending mainly on the loading scheme, but in most cases it is between 500 °C and 620 °C.
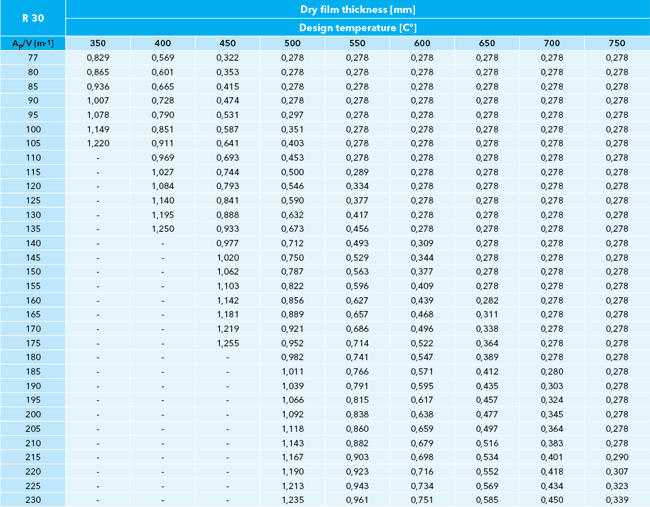
The required thickness of the fire protective reactive coating depends on the fire resistance, the designed critical temperature of the steel structure and the Ap/V ratio. The necessary dry film thicknesses (without the primer and the topcoat of any thickness) are listed in the related tables (for fire resistance of more than R 120, please contact the Promat Technical department. For concrete, the critical state is linked to the critical temperature of the reinforcing bars (normally from 250 °C to 500 °C) and the reaching of a temperature of 500 °C inside the concrete element.
Preparation and application
Reactive coatings require a greater degree of environmental monitoring than conventional fire protective products. Water-based coatings are generally moisture sensitive and must be protected against high humidity, rain and consequent water ponding, particularly during onsite application, with appropriate topcoats, otherwise blistering and/or delamination could occur. Application conditions should be within the following limits during application and drying of the material, with readings recorded a minimum of twice daily, at the beginning and end of the working day:
- The substrate should be clean, dry and free of any dust, loose scaling, loose rust, oil and other release agents that prevent good adhesion. A compatible primer must be applied before the application of the intumescent coating.
- PROMAPAINT® should be applied when the temperature of the substrate and the ambient air temperature is at least 10 °C or more. This temperature should be maintained 24 hours after application. The maximal temperature of the substrate and ambient air temperature should not exceed 35 °C. The relative humidity should not exceed 80 %.
- The surface must be dry and the surface temperature must always be a minimum of 3 °C above the dew point. In line with good painting practice, application should not take place in conditions which are deteriorating, e.g. where the temperature is falling and is likely to go below 10 °C, or where there is a risk of condensation forming on the steel.
- PROMAPAINT® shouldn’t be applied if condensation is present on the steel to be coated.
Airless spray equipment is the preferred method for speed and uniformity of finish. Application by brush or roller is a suitable method, but is generally recommended for small areas and repairs only. Use a high-grade latex paint brush or a short pile roller. The appearance of brush or roller applied products will be different to that of the spray applied coating, which will provide the smoothest finish.
Future inspection and maintenance
The fire protection properties of the intumescent systems will remain as long as the integrity of the coating is maintained and there in no degradation of the material. Regular inspections of the fire protection system should be carried out. Any damaged areas, defects, etc. must be repaired as recommended in the application guidelines. Inspection intervals for a project should be stated in the specifications. Typically, inspections should be carried out every two years, after the durability/working lifetime (note: durability is related to a specific exposure conditions and will be project specific). PROMAPAINT® coatings have been tested for the maximum durability, according to ETAG 018-2.
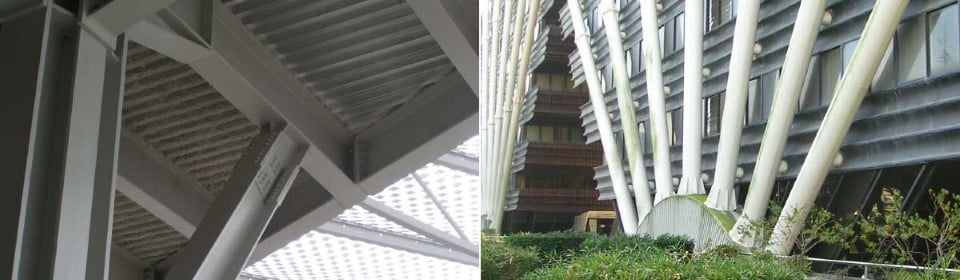
Extraordinary maintenance interventions, i.e. in case of damage to the intumescent system due to mechanical action, water adsorption, voluntary removal, etc., must be carried out immediately. Topcoats must be maintained as a continuous film to protect PROMAPAINT® products from the environment, when necessary. However, excessive build-up of topcoat thickness could be detrimental to the fire protection system and must be avoided. As a guide, the maximum recommended number of topcoats is three, applied at 30 microns DFT per coat (the total thickness cannot exceed 90 microns, irrespective of the number of layers of topcoat applied).
Given all the specifics, regulations and requirements, knowledge of the materials is required in order to properly apply the chosen protective coating. For the protection system to properly function in the event of a fire all the manufacturer's instructions must be taken to account. The thickness of the coatings is very important, and thus only specially trained teams can handle the application.