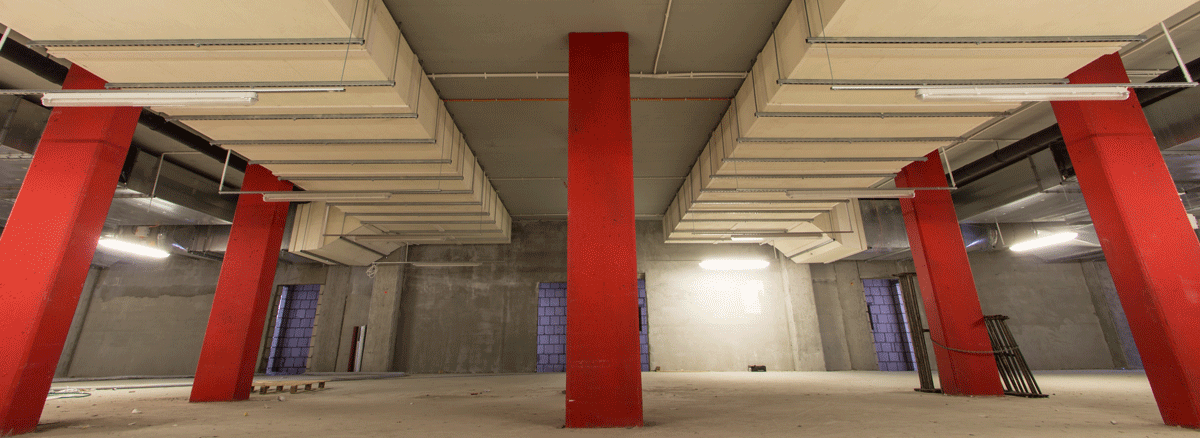
Fire rated ductworks are very important element of fire safety system in buildings. Depending on its role, we can distinguish two main types: smoke extraction ductworks and ventilation ductworks.
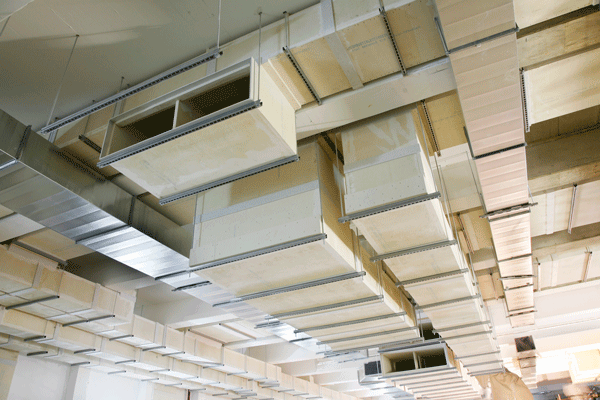
Smoke extraction ductworks
Smoke extraction ducts are used to remove smoke from buildings, to enable emergency evacuation of the occupants as well as improved firefighting and flash over prevention.
They are mainly used in large compartment, car parking, high-rise building and atriums in commercial, office and residential buildings. Car parks with low ceilings present dangerous zones because the smoke layer can fill the space very quickly and prevents evacuation. High compartments (typically greater than 15 m) are vulnerable to spreading smoke and present a challenge for fire protection engineers because of the decreased effectiveness of automatic sprinkler systems.
Fire rated ductworks are required to conduct the smoke outside from the building, even using fan assisted systems. If a smoke extraction ductwork is wholly contained within a fire compartment, it must at least be capable of resisting the anticipated smoke temperatures generated during the development of a fire. If the ductwork penetrates a fire resisting barrier (such as a fire rated partition or ceilings), it must also be capable of providing the same fire resistance of the barrier.
From an effective smoke removal point of view, it is necessary to subject the room in question to a detailed analysis in terms of the fire propagation velocity, floor surface area, and height.
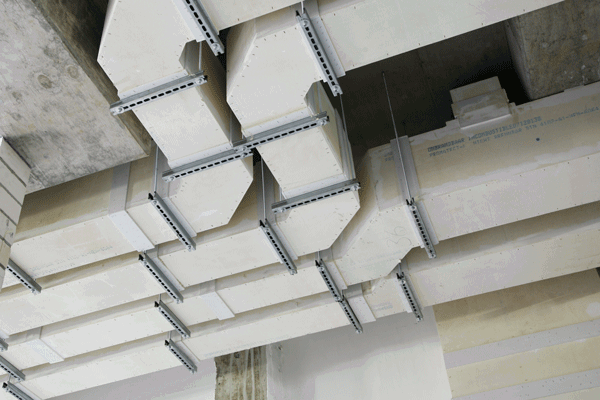
Fire rated ventilation ductworks
Fire rated ductworks are used to guarantee the fire compartmentation. More precisely, fire rated ventilation ducts can avoid fire and heat spread between two compartments.
It is possible to prevent fire spread from one fire compartment to another, along stairways, rooms and general access corridors, only if all building materials and structural elements share a common fire classification and fire resistance rating.
Compartment walls and floors must have a certain fire resistance, which means that the performance criteria of load-bearing capacity (stability), integrity and insulation have been met for a duration of 30 to 240 minutes. It is therefore extremely important that, where compartmentation boundaries are penetrated by services, the fire separation criteria for the penetrated elements are maintained and, in particular, that ducting should not become a conduit along which fires, or hot smoke, may spread to other areas.
The view on risk of smoke spread in ventilations systems varies throughout Europe. In some countries smoke spread via the ventilation system is not considered to be a problem at all, in other countries smoke dampers or fire/smoke dampers are always required where there are more than one fire compartment supplied by the same system. Finally, there are countries where the regulations in addition to fire/smoke dampers also allow performance-based design.
In any case, the fire performance of a duct which penetrates a fire resisting/separating element must requires careful consideration by specifiers. Typical metal sheet ducts fail to meet internationally accepted fire protection requirements. They heat and deform rapidly from the effects of fire. Under specific circumstances they can even accelerate the spread of flame and smoke.
What is the best ductwork system for my project?
Choosing the right fire rated ductwork is difficult due to complexity of the duct construction (passing through different fire compartments), function of the system in the ambient and fire conditions.
Promat offers a wide range of solutions for both ventilation and smoke extraction – for different operating pressures, sizes, orientations, configurations, even for partial fire exposures. The solutions developed by our technical experts can meet any fire resistance requirement from 30 minutes (E – or EI 30) up to 120 minutes (E – EI 120), including smoke leakage (S). For special cases 240 minutes integrity solutions are also available.
Traditionally, all ductwork used to be fabricated from steel. It required to be encased in a fire protection system when passing through a compartment wall or floor without the aid of a fire damper, or when used as part of a smoke extraction system. Promat has developed self-supporting systems without a steel liner, for example PROMATECT®-AD, PROMATECT®-L500 and MASTERBOARD® gwhich can match the leakage and air flow performance of steel ducts both for air duct and smoke extraction ducts.
Main advantages:
- No steel sheet ducts are required
- Single layer construction
- Dimensionally stable and moisture resistant
- Easy to cut to size, ex factory or on site
- Lightweight shaped sections
- Serviceable smooth surface, robust
- Tested according to the most severe international standards
- Supporting hangers, supports and their fixings can be unprotected
- Big dimensions (maximum dimensions are all classified by authorized laboratories)
- Roughness factor of the surface substantially identical to steel
- Promat calcium silicate boards have got CE marking for intended use Type 9: Technical services assemblies in buildings.
The acoustic performances and the room temperature thermal insulation of Promat ductworks can be even improved using additional layer of mineral wool and/or plasterboards.
PROMATECT® boards can be used also for cladding of existing steel ducts.
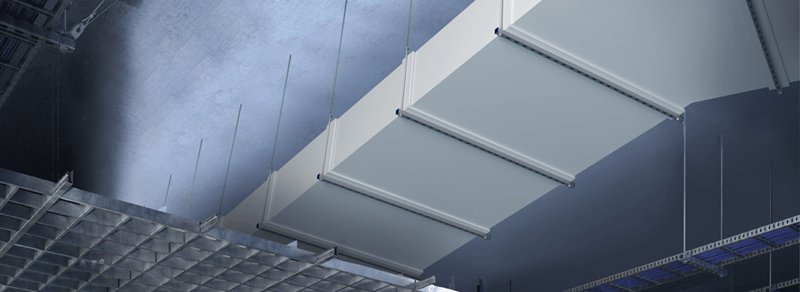
How are the smoke extraction ducts tested?
Smoke extraction ducts can be tested according to different standards. The most common are European Standard (EN 1366), British Standard (BS 476) and, in some specific cases, American Standard (UL).
Regarding Europe, the smoke extraction ducts are tested with fire from inside and outside.
Regarding smoke control ducts, can be distinguished:
- single compartment smoke control ducts, which can be used in one fire compartment only and are tested according to EN 1366-9, under 300°C or 600°C time/temperature curve (The heating conditions and the furnace atmosphere shall conform to those specified in EN 1363-1 until 300°C or 600°C is reached. After this temperature shall be maintained for the rest of the test) and classified according to EN 13501-4 in Europe
- multi compartment fire resistant smoke control ducts, which can be used in any number of fire compartments and are tested according to EN 1366-8, under ISO 834 curve (EN 1363-1) and classified according to EN 13501-4 (as “duct C”)
These method of test are only suitable for ducts constructed from non-combustible materials (class A1 and A2-s1, d0).
The test method for multi compartment fire resistant smoke control ducts (EN 1366-8) is applicable to fire resisting ducts that have already passed the appropriate period to EN 1366-1 (Ducts A/500 Pa and B). For mono compartment ducts, only test according to EN 1366-9 is required.
The performance criteria are the followings:
- Smoke leakage (S): the duct shall not have a leakage exceeding 5 m³/h per 1 m² of internal surface area. This shall be related to the surface area of the duct from the perforated plate to the end of the duct by the inlet nozzles.
- Integrity (E): the integrity at the seal/penetration between the duct and the supporting construction shall be judged in accordance with EN 1363-1.
- Insulation (I): test results from EN 1366-1 shall demonstrate the insulation performance of the duct.
- Reduction in cross-section: the internal dimensions (width and height for rectangular ducts, diameter for circular duct) of the smoke extracting ductwork shall not decrease by more than 10 % during the test.
- Mechanical stability: if the duct inside the furnace collapses, so that it can be judged as not being able to maintain its smoke extraction or fire resistance function, this shall be regarded as failure under the mechanical criterion.
How are the ventilation ductworks tested?
Ventilation ductworks can be tested according to different standards. The most common are European Standard (EN 1366), British Standard (BS 476) and, in some specific cases, American Standard (UL).
In Europe, ventilation ducts are tested according to EN 1366-1 and classified according to EN 13501-3. The classification is completed by ‘(i → o)’, ‘(o → i)’, or ‘(i ↔ o)’ to indicate whether the element has been tested and fulfils the requirements with fire from the inside or outside only or both.
In fact, the test is divided into two fire scenarios, fire from outside of the duct and fire from inside of the duct. One duct is needed for each scenario and both scenarios have to be tested in horizontal and vertical direction.
The standard heating curve described in EN 1363-1 (ISO 834) is used for both scenarios.
The performance criteria are the following:
- Integrity (E): integrity failure shall be deemed to have occurred if any of the following are observed:
- integrity failure on the unexposed side as defined in EN 1363-1,
- the volume flow rate measured in duct A exceeds 15 m³ /(m² h), related to 20°C and 1013 mbar, related to the internal surface area of the duct inside the furnace.
- Insulation (I): insulation failure shall be as defined in EN 1363-1: The duct does no longer satisfy the Insulation criteria if the temperature rise on the unexposed side exceeds 180 °C on any of the thermocouples or 140°C in average.
- Smoke leakage (S): failure of this criterion shall have occurred if the flow rate in duct A during the test exceeds 10 m³ /(m² h), related to 20°C and 1013 mbar, related to the internal surface area of the duct inside the furnace.