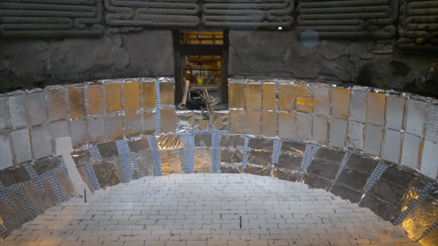
Steel production, nowadays, takes revolutionary steps towards the "greener future". In the traditional approach, the journey begins with iron ore and coal, with the former being transformed into pig iron in blast furnaces, and the latter turned into coke in coke oven batteries. This is followed by melting in Basic Oxygen Furnaces (BOFs), a process known for its high energy consumption and substantial carbon emissions. To address these issues, there is a growing shift towards Electric Arc Furnaces (EAFs) in steelmaking.
The transition from Oxygen steelmaking to Electric steelmaking is motivated by the need to reduce energy consumption and carbon footprint. This is where Promat’s role comes into play. Our energy-saving insulation solutions are designed to minimize heat losses, enhance the efficiency of heat input, and reduce the tap-to-tap time. These improvements result in a notable decrease in EAFs' electric energy consumption and emissions.
Our insulation solutions are mainly based on microporous products complemented by fiber materials and insulation refractory fire bricks (IRFBs). Microporous materials are known for being lightweight and thin, which is beneficial for steelmakers as it allows for the maintenance of optimal refractory lining proportions. The preferred solution is to have a thicker face lining composed of refractory materials and the thinnest possible insulation lining. This combination not only contributes to the efficiency of the process but also aligns with the objectives of reducing energy consumption and environmental impact in the steelmaking industry.