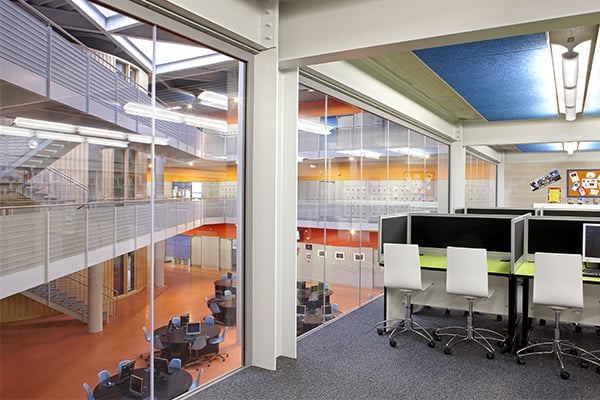
By Cath McLean, Segment Manager for glass at Promat UK
Dame Judith Hackitt’s assertion that the building industry routinely puts cost before quality will come as no surprise to architects and contractors who often see their specifications being challenged, and ultimately changed, just to save a few pounds. Whilst this ‘value engineering’ can deliver what it promises for clients – better value from their investment – it has become synonymous with an industry obsessed seeking to do everything at the lowest possible cost.
Quality is critically important for fire resistant glazing installations because there is no margin for error. Every element needs to be dependable in providing consistency in its performance capabilities and standard of manufacture. The origin of the glass, framing materials and other components must be evaluated and scrutinised at the product specification stage. Choosing a supplier, therefore, like Promat UK, which manufactures to internationally renowned quality standards like ISO 9001: 2015 and ISO 14001: 2015, offers an additional layer of assurance.
And once specified, passive fire protection products must stay specified, as the slightest change to the specification can compromise the expected level of fire resistance. This is why Promat UK has invested the ‘Specified for a Reason’ phrase as a trademark – this needs to be kept front of mind when other project pressures make a change to the spec appealing.
But every application is different, so this means the specification must be carefully tailored to ensure the glazing delivers the necessary protection for people and assets. It is a process which starts with five basic questions.
1. What classification of fire performance is required?
Fire resistant glazing typically provides protection for a period of 30, 60, 90, 120 or 180 minutes. This figure will be displayed next to the type of protection provided - Integrity only (E), Radiation control (EW) and Integrity and Insulation (EI). So, if the glass is integrity only and provides 30 minutes’ protection, it will be classified as E30.
2. Which glazing frame material is being used?
The specification needn’t be determined by having to use a certain type of frame to meet the fire performance classification. However, whichever framing material is chosen, the glass, beading and setting blocks must all suitable to avoid the performance being compromised and leading to catastrophic failure. The component parts don’t work in isolation so should be tested as a complete, certified system.
Different framing materials – including calcium silicate (PROMATECT® H), timber, steel and aluminium, however, may determine the maximum sizes that the glazing can go up to. For example, a steel frame may allow for a larger expanse of fire resistant glass than timber.
3. What are the glass sizes?
Generally speaking, every type of glass will be tested to a maximum height and width, ultimately determining the size or configuration of the glazing that is possible. These maximum heights and widths usually cannot be exceeded, and the height/width ratio must be retained – with some exceptions. Check with your glass supplier and, importantly, keep within the tested dimensions and do not exceed the maximum area of the glazing.
4. What is the application?
Application type has a major bearing on which fire glass is suitable. Consider the implications of using the different glass types for internal or external applications and the specific requirements applying to doors and partitions. Every application will demand its own mix of functionality, such as impact resistance, acoustic insulation or aesthetic goals, which will determine the most suitable glass choice. The glass must be specified in accordance with whether it has been tested for vertical, horizontal or sloping applications.
**5. Is single or double glazing required? ** The final question is whether single or double glazing is required, which may be determined by other functionality. For example, an internal glazed screen may also need to provide an acoustic barrier, in which case that might need to be double glazed. External applications may also need to be double glazed to meet thermal objectives.
Avoid the risks
These five questions provide the starting point when designing and specifying a fire resistant glazing solution, but as the multiple factors to each of these illustrates, it is a complex area. Many factors can affect a specification’s effectiveness in stopping the spread of fire, so seeking expert advice from your glazing supplier is the only way to be confident of success. But also keep quality in mind, and don’t be tempted to fall into the ‘cheapest will do’ trap if a product’s stated performance seems adequate.