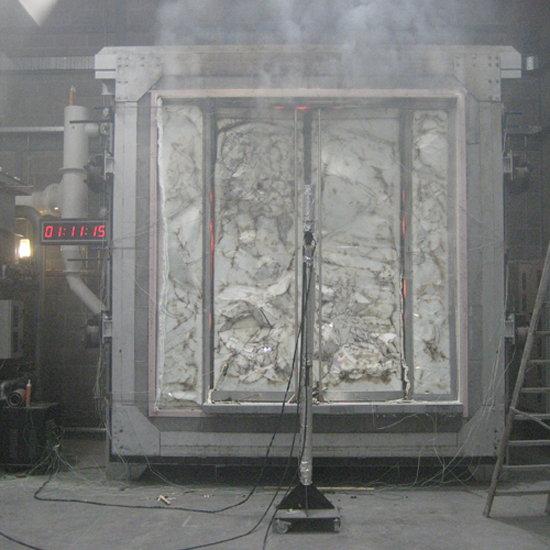
By Cath McLean, Segment Manager for glass at Promat UK
With so much confusion and uncertainty prevailing about how to deliver assured fire protection, it is worth remembering that two factors matter more than most when making design and specification choices – product testing and traceability.
Delivering assured passive fire protection in glazing installations demands a clear understanding of how a product or complete system has been tested or assessed and deemed to have achieved the claimed standard, plus credible traceability for the origin of all the products combined and installed. If a solution is being considered that does not provide concrete evidence on both fronts, an element of risk is being introduced that could result in catastrophic consequences. You may end up with products that haven’t actually been tested in a given application and, therefore, it is impossible to guarantee performance in the event of a fire.
A test is a test is a test, isn’t it?
The Hackitt Review called out the confusing myriad of British and European standards, plus the Building Regulations, relating to the design of fire protection measures in UK buildings. However, establishing the most suitable fire protection solutions is made more complicated for specifiers because of the different methods of testing and assessment available for product manufacturers and installers to demonstrate fire rating performance.
All methods do originate with a test conducted to BS 476 or BS EN 1364 parts 1-4, and BS EN 1634-1:2008 specifically for doors. But there are some important differences between the five main routes used to provide evidence of compliance, which need to be understood to enable a confident, informed judgement to be made about the specification.
It is vital to remember, as the latest guidance from the Passive Fire Protection Forum (PFPF) underlines, ‘assessments should not be regarded as a way to avoid a test where one is necessary. They should only be carried out where sufficient relevant test evidence is available. Relevant test evidence is unlikely to be provided by test standards which have different classification criteria.’
Primary test report
The most obvious way to demonstrate product performance is through a specific test report from a UKAS-accredited or notified European test laboratory.
Here, raw data is published from a physical test in which a product or complete assembly is built and burned. The test can be conducted privately or via a third party accredited test facility, but test reports are often confidential due to the IP content and cannot be used without the sponsor’s permission. Closed tests ideally need some evidence of external replication to provide assurance.
Assessment report
Assessment reports are used in lieu of a test report to criteria determined by the PFPF (Passive Fire Protection Forum) with the overriding premise being that the assessed performance would be achieved if the construction were tested.
Assessments can only be made by appropriately qualified persons and are useful for a range of variants to systems when testing would simply be impractical and uneconomical. In every case, the assessment will be made taking into consideration the specific variation in relation to the standard and any available test evidence.
Field of application report
A field of application report is appropriate when an extension to a product is deemed to be slight and, therefore, representative of expected performance for very specific applications, and with strict scope and conditions attached. The manufacturer will be clear about the range of situations in which their product can be sold. They can send the field of application report with the product, so ensuring that the company installing it understands where and how they can install the product.
Classification report
A classification report would be written by an accredited body to provide a summary of the data from a test, including information on products and performance. Again, certain data may be redacted for IP reasons, but a classification report is accepted as proof of performance.
Third party accreditation
Third party accreditation under schemes such as the BM TRADA Q-Mark and Certifire offer independent monitoring along the supply chain to ensure standards are being upheld at every stage. These schemes have requirement for systems and products to be included which go over and above the fire test, with membership dependent on product sampling when testing, FPC audits and production controls, as well as a product recall procedure should this be required. Membership is subject to ongoing compliance and this means scrutiny of the whole supply chain, which is where management systems such as ISO 9001 and ISO 14001 play a vital role. To ensure correct installation the installer should also hold some training certification which may be system-specific, or industry recognised such as FIRAS.
Track and trace
All of the report approaches above form the compliance governance of what can be used together. Having worked hard to get the products tested, traceability of components is the next consideration to ensure the final installed product will perform as promised.
Traceability – ‘the quality of having an origin or course of development that may be found or followed’ – is important to establish the pedigree of a product and to ensure it has been sourced correctly. Having traceability helps to prevent product substitution and, as all items are known from source, they are easier to replace or recall if a problem arises.
The peace of mind provided by having proof of attributes of the materials being supplied cannot be underestimated. The transparency and clarity afforded by traceability in the supply chain is valuable in fostering loyalty, trust and confidence amongst customers and end-users, as well as allowing for easy benchmarking if alternatives are being considered and enabling the tracking of production.
Such is the importance of traceability that Promat UK has invested significantly in its products and procedures over the past two decades. The Promat SYSTEMGLAS® fire rated glazing system, for example, is manufactured and processed in-house, with inspections carried out by Promat glazing specialists once installed to ensure the correcting fitting methods have been adopted.
Ultimately understanding how the various testing, assessment and accreditation methods work, which all have an important place in the passive fire protection supply chain, and specifying traceable products, provides a clear picture on the capabilities and expectations from an installation. Further design, specification and installation advice on how to arrive at the best solution for the application is available from Promat UK.